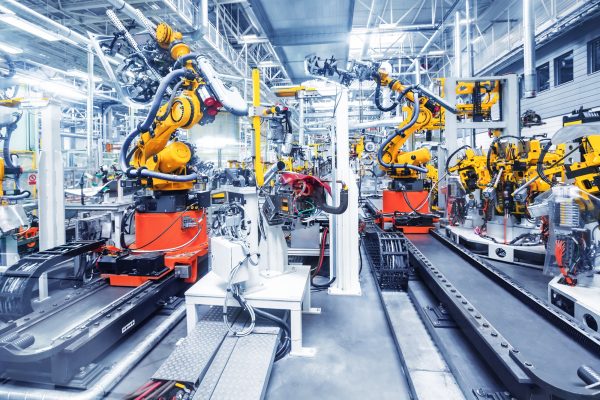
Produktion: Aufgaben, Ziele und Produktionsfaktoren
Was versteht man unter dem Begriff Produktion?
Als Produktion definiert man im Allgemeinen die Fertigung von Gütern und Dienstleistungen. In der Betriebswirtschaftslehre und in der Volkswirtschaftslehre und somit in der Produktionstheorie versteht man unter Produktion oder Herstellung einen Prozess, bei dem verschiedene Produktionsfaktoren und Rohstoffe in einem Transformationsprozess kombiniert werden, bis ein neues Konsum- oder Investitionsgut oder eine Dienstleistung als Endprodukt entsteht.
Der Begriff Produktion umfasst alle Aktivitäten, die zur Herstellung eines Produkts oder einer Dienstleistung erforderlich sind. In der Betriebswirtschaftslehre gehört die Produktion neben der Beschaffung und dem Absatz zu den drei wesentlichsten Unternehmensbereichen im Rahmen der Leistungserstellung.
In der Produktionstheorie beinhaltet die Produktion die Planung der Produktionsprozesse, die Organisation der Produktionsressourcen, die Überwachung und Kontrolle der Fertigung sowie die Evaluierung des wirtschaftlichen Produktionsergebnisses.
Was sind die Aufgaben der Produktion?
Der Prozess der Produktion umschließt drei essenzielle Aufgaben:
- Der Produktionsplanung,
- Der Produktionssteuerung,
- Der Produktionsdurchführung
Die Produktionsplanung
In der Phase der Produktionsplanung werden die verschiedenen Aspekte der Produktion koordiniert. Zur Produktionsplanung gehören:
- die Bestimmung der Produktionsmenge,
- das Festlegen der Produktionsabläufe,
- die Organisation der Arbeitskräfte,
- die Beschaffung von Produktionsmitteln und
- die Analyse vom Primärbedarf eines Produktes.
Aus dem Primärbedarf, der die Kundennachfrage beschreibt, kann im nächsten Schritt der Sekundärbedarf bestimmt werden. Dieser sagt aus, wie hoch der Materialbedarf für die Produktion ist. In dieser ersten Phase der Fertigung wird in der Prozessplanung ebenfalls aufgegliedert, wie der Produktionsprozess optimiert werden kann.
Die Produktionssteuerung
Im zweiten Schritt folgt die Produktionssteuerung. In dieser Phase wird sichergestellt, dass der gesamte Produktionsprozess internen und externen Anforderungen entspricht und reibungslos verläuft. Die Produktionssteuerung ist dafür zuständig, die vorgesehenen Produktionsschritte umzusetzen. Zu ihren Aufgaben gehören die Überwachung der Produktionsabläufe und die Kontrolle der Qualität. Die Produktionssteuerung sorgt zusammenfassend dafür, dass die Leistungserstellung effizient, zuverlässig und wirtschaftlich erfolgt.
Die Produktionsdurchführung
Die Produktionsdurchführung ist der letzte Schritt und beschreibt die praktische Leistungserstellung in der Produktion. In dieser Phase werden die Produkte oder Erzeugnisse hergestellt und an die Kunden geliefert. Die Produktionsdurchführung ist entscheidend für den wirtschaftlichen Erfolg eines Unternehmens. Sie sorgt dafür, dass die Produkte rechtzeitig und in einwandfreiem Zustand geliefert werden.
Was sind die drei Produktionsfaktoren?
Jedes Produkt oder jede Dienstleistung muss in einem aufeinander abgestimmten Produktionsprozess hergestellt werden. Die Produktionsfaktoren Arbeit, Boden und Kapital sind die Grundlagen für die Produktion von Gütern und Dienstleistungen. Sie stellen die Ressourcen bereit, aus denen Unternehmen Produkte herstellen können.
Arbeit ist ein wesentlicher Faktor in der Produktion, da sie die physischen und intellektuellen Kräfte bereitstellt, die für die Herstellung von Produkten und Dienstleistungen erforderlich sind. Die Mitarbeiter eines Unternehmens sind das Rückgrat jedes Produktionsprozesses. Sie nutzen entweder Werkzeuge und Maschinen oder ihre intellektuellen Fähigkeiten. Gezielte Fachfortbildung kann die Qualität der Arbeit erhöhen.
Der Boden ist ebenfalls ein entscheidender Produktionsfaktor, da er die Räume und die natürlichen Ressourcen bereitstellt, aus denen Produkte hergestellt werden. Zur begrenzten Ressource Boden gehören unter anderem das Wasser, die Luft und das Sonnenlicht. Werden Vorprodukte weiterverarbeitet, wird der Produktionsfaktor Boden aus betriebswirtschaftlicher Sicht eingekauft.
Das Kapital ist der dritte Produktionsfaktor. Es stellt die finanziellen Mittel bereit, die für die Produktion von Gütern und Dienstleistungen erforderlich sind oder bedient sich Maschinen oder Patenten zur Produktion. In der klassischen Betriebswirtschaftslehre spielt das Kapital keine Rolle für die Produktion. In unserer modernen Welt ist eine Fertigung ohne Kapital nicht vorstellbar, sodass es als dritter Produktionsfaktor angesehen werden kann.
In der Produktionstheorie stellen die Produktionsfaktoren Arbeit, Boden und Kapital die Grundlagen für die Leistungserstellung von Gütern und Dienstleistungen dar.
Welche Produktionsarten gibt es?
Man unterscheidet verschiedene Produktionsarten:
Massenproduktion | Herstellung großer Mengen eines Produkts mit standardisierten Verfahren und Maschinen. |
Chargenproduktion | Die Herstellung größerer Mengen eines Produkts in kleineren Chargen. Diese Produktionsart ermöglicht mehr Flexibilität bei der individuellen Gestaltung und kann bei bestimmten Produkten (z. B. Arzneimitteln) effizienter sein als die Massenproduktion. |
Kontinuierliche Produktion | Herstellung eines Produkts ohne Unterbrechung in einem kontinuierlichen Flussverfahren. |
Fließbandfertigung | Durchlaufen einer Reihenfolge von Stationen im Herstellungsprozess. Jede Station ist für eine andere Aufgabe zuständig ist. Unterart der Massenproduktion, die für Produkte (z. B. Fahrzeuge) verwendet werden kann, die viele verschiedene Schritte in ihrem Produktionsprozess erfordern. |
Schlanke Produktion (Lean Production) | Herstellungsmethoden, die darauf abzielen, Verschwendung zu minimieren und die Effizienz zu maximieren. Dabei können Techniken wie Just-in-Time-Produktion oder Kaizen zum Einsatz kommen. |
Six Sigma | Herstellung eines Produkts mit minimalen Fehlern unter Verwendung einer Vielzahl von Qualitätskontrollmethoden. |
Agile Fertigung | Herstellung eines Produkts unter Verwendung von Methoden, die darauf abzielen, flexibel zu sein und auf Veränderungen zu reagieren. |
Projektfertigung | Individuelle Herstellung nach einem spezifischen Projektplan, beispielsweise bei einem Kreuzfahrtschiff. |
Was sind die Ziele der Produktion?
Bei der Produktion verfolgen produzierende Unternehmen je nach Industrie diverse Ziele:
Mengen-optimierte Produktion
Mengen-optimierte Produktion ist eine spezielle Form der Produktion, die auf die Optimierung der Produktionsfaktoren abzielt. Diese Methode wird häufig in Unternehmen angewendet, die sich auf die Herstellung von Massenprodukten konzentrieren. Ziel der mengen-optimierten Produktion ist es, Kosten zu sparen und die Effizienz zu steigern.
Wirtschaftliche Produktion
Die meisten Unternehmen fokussieren eine wirtschaftliche Produktion nach dem Maximalprinzip. Ziel ist es, mit geringen Herstellungskosten und hohen Deckungsbeiträgen die bestmögliche Rentabilität zu erzielen.
Soziale Produktion
Unternehmen, die eine soziale Produktion als Ziel ausgeben, sind mitarbeiterorientiert. Sie achten auf Sicherheitsstandards, Work-Life-Balance und professionelle Arbeitsbedingungen und sind darauf bedacht, ihre Mitarbeiter individuell zu fördern. Das Lieferkettengesetz in Deutschland zielt darauf ab, soziale Standards in Ländern sicherzustellen und auszubauen, in denen deutsche Unternehmen produzieren.
Ökologische Produktion
Bei der ökologischen Produktion achten Unternehmen darauf, umwelt- und ressourcenschonend zu produzieren. Der ökologische Fußabdruck eines Produkts sollte möglichst gering sein. Viele Unternehmen geben für die nahe Zukunft ökologische Ziele an, zum Beispiel Zero C02.
Qualitative Produktion
Bei der qualitativen Produktion müssen die Produktionsprozesse ständig überwacht und optimiert werden. Ziel ist es, eine hohe Qualität zu gewährleisten und die Qualität der hergestellten Produkte fortlaufend zu verbessern.
Temporäre Produktion
Unternehmen, die eine temporäre Produktion fokussieren, verfolgen das Ziel, ihre Produkte möglichst schnell herzustellen und auszuliefern. Kurze Produktionszeiten, getaktete logistische Abläufe und optimale Prozesse helfen, die Produktionszeiten signifikant zu verringern.
Wie entwickelt sich die Produktion in Deutschland?
Betrachtet man die reale, preisbereinigte Produktion in Deutschland seit 2012, fällt auf, dass diese sich bis zum Beginn der Corona-Pandemie im Jahr 2020 fortlaufen erhöht hat. Nach dem Einbruch durch die Einschränkungen durch Covid-19 hat das produzierende Gewerbe bis Februar 2022 kalenderbereinigt nahezu das Vorkrisenniveau erreicht. Nach dem Statistischen Bundesamt stieg die Produktion im Juni um 0,8 % zum Vormonat, sank im Juli jedoch wieder um 0,3 %, ebenfalls im Vergleich zum Vormonat.
Durch den Ausbruch des Krieges in der Ukraine und dessen Folgen sinkt die Fertigung in Deutschland signifikant. Insbesondere in energieintensiven Industrie-Branchen verdeutlicht das Statistische Bundesamt einen merklichen Rückgang. In entgegengesetzter Weise entwickelt sich das Baugewerbe. Die folgende Abbildung des Statistischen Bundesamtes zeigt die kalenderbereinigte Entwicklungen des produzierenden Gewerbes.
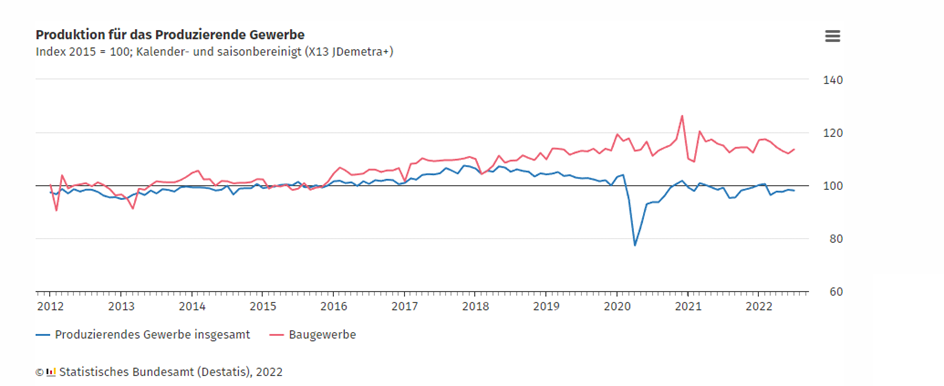