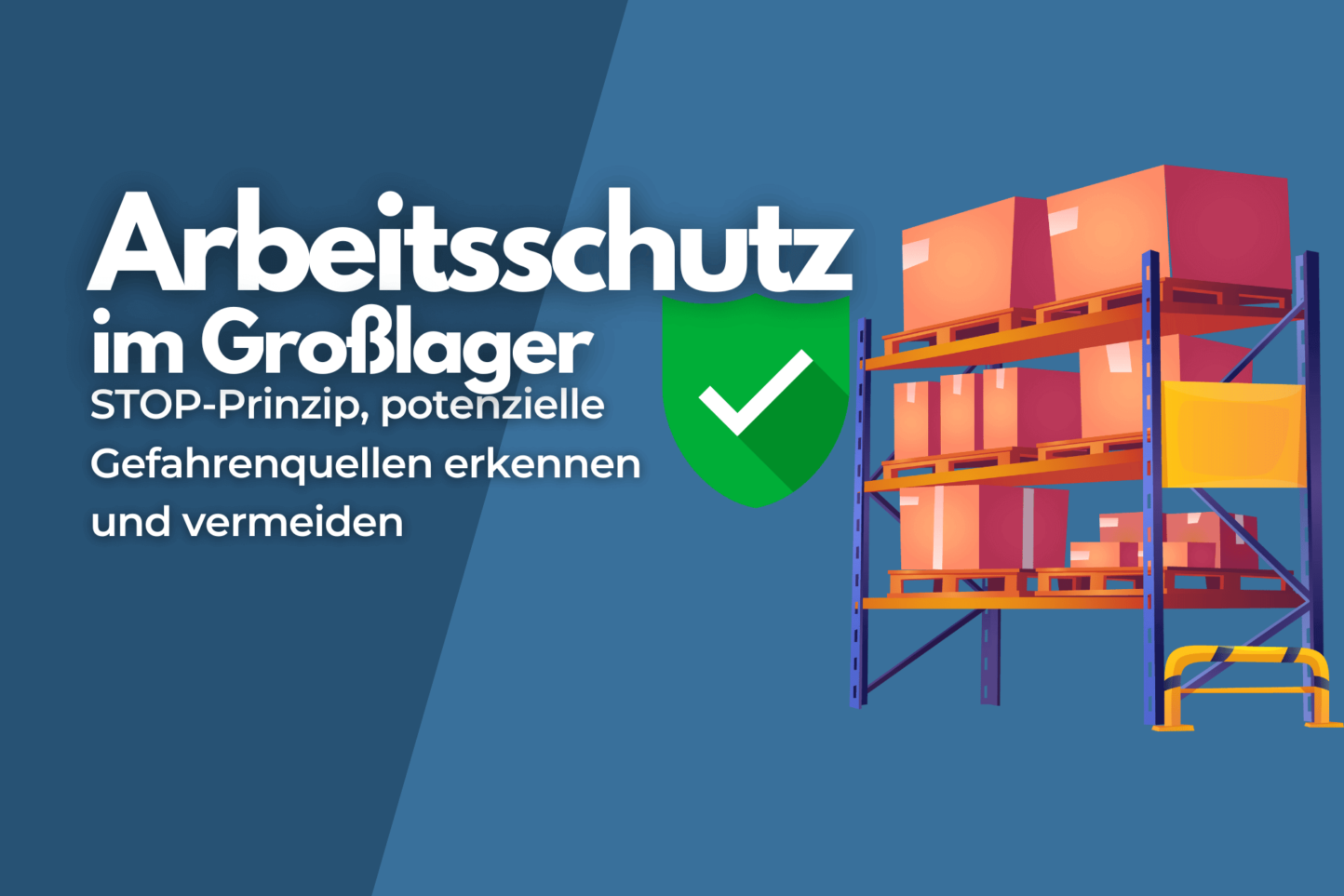
Arbeitsschutz im Großlager: Worauf ist zu achten?
Diese potenziellen Gefahrenquellen lauern im Großlager
Der Gesetzgeber verpflichtet den Betreiber eines Großlagers dazu, die möglichen Gefährdungen zu ermitteln und entsprechende Schutzmaßnahmen durchzuführen. Eine solche Gefährdungsbeurteilung ist Pflicht und muss sämtliche Arbeitsbereiche des Lagers umfassen. Zu den typischen Gefahren gehören:
- Wegrollende und herunterfallende Gegenstände: Bei der Beladung von Regalen entsteht die Gefahr, dass Waren fallen oder sich unerwartet bewegen. Die Einhaltung von maximalen Stapelhöhen und die Absicherung von Regalen ist eine Pflicht des Lagerbetreibers
- Gefährliche Flüssigkeiten: Der Umgang mit Gefahrenstoffen unterliegt besonderen Sicherheitsvorkehrungen. Mitarbeiter müssen Zugriff zu persönlicher Schutzausrüstung haben. Darüber hinaus muss der Lagerinhaber sicherstellen, dass gefährliche Stoffe bei einem Leck zurückgehalten werden.
- Mitarbeiterbedingte Gefahren: Der Gefahrenfaktor Mensch ist auch im Lager eine Herausforderung. Durch Unterweisungen und Schulungen lassen sich Risiken deutlich minimieren. Die Einhaltung der Arbeitsschutzmaßnahmen im Großlager muss regelmäßig vom Arbeitgeber überwacht werden.
- Mechanische Gefahrenquellen: Fördertechnik, Flurförderzeuge und Hubtechnik bergen mechanische Verletzungsrisiken. Regelmäßige Wartungen, Unterweisungen und die Absicherung von Leitern, Rampen und Treppen tragen zur Reduktion des Unfallrisikos bei.
Bei vielen Tätigkeiten müssen Sicherheitszeichen angebracht werden, beispielsweise beim Betrieb von Flurförderfahrzeugen, aber auch im Handling mit Gefahrengütern. Diese Sicherheitsmarkierungen dienen dem eindeutigen Hinweis auf Gefahren und sind (je nach Situation) verpflichtend! Sie müssen gut sichtbar und allseits verständlich sein. Bestimmte Hinweise dürfen nicht einfach auf einen Zettel geschrieben werden. Es gibt eindeutige Sicherheitszeichen, die vom Gesetzgeber vorgeschrieben sind.
Schutzmaßnahmen nach dem STOP-Prinzip integrieren
Das STOP-Prinzip hat sich in der Logistik bewährt. STOP steht dabei für Substitution, Technik, Organisation und Personal. In all diesen Bereichen gibt es Möglichkeiten und Denkansätze, wie Lagerbetreiber die Sicherheit erhöhen können.
- Substitution: Ist es möglich, einen Rohstoff auszutauschen oder auf eine gefährdende Maschine zu verzichten? Substitution steht für „Tausch“ bzw. „Ersatz“ und kann bereits zur Gefahrenminimierung beitragen.
- Technische Maßnahmen: Sind bauliche Veränderungen in der Lage, die Gefahren zu reduzieren oder einzudämmen? Wenn ja, sollten diese technischen Optimierungen genutzt werden.
- Organisatorische Abhilfe: Lässt sich die Sicherheit der Mitarbeiter durch eine Umstrukturierung der Arbeitsabläufe steigern?
- Personenbezogene Maßnahmen: Können bestimmte Ausrüstungsgegenstände und Schutzvorkehrungen dazu beitragen, Besucher und Angestellte noch effizienter vor Gefahrenquellen zu schützen:
Tipp: Die Umsetzung des STOP-Prinzips erfolgt direkt nach dieser Reihenfolge. Im ersten Schritt gilt es, das ungefährlichste Gerät zu suchen und erst dann kommen technische, organisatorische und personenbezogene Maßnahmen zum Einsatz.
Tipps zur Reduktion von Gefahrenquellen in der Lagerlogistik
Bis die Ware beim Versender angekommen ist, hat sie einen langen Prozess der Lagerung und Logistik hinter sich. Gesetzliche Vorschriften sind durch jeden Lagerinhaber zu erfüllen, bei Nichteinhaltung drohen empfindliche Strafen. Darüber hinaus gibt es nicht zwingend vorgeschriebene Maßnahmen, mit denen sich die Risiken für die Mitarbeiter minimieren lassen. Ein effizientes und sicheres Lager ist nicht nur im Hinblick auf die Gesetze sinnvoll, sondern auch für den Arbeitsworkflow. Mit den nachfolgenden Tipps schaffen Lagerlogistiker ein sicheres Arbeitsumfeld und tragen dazu bei, die Unfallquote zu reduzieren.
Flurförderfahrzeuge sicher einsetzen
Das Flurförderfahrzeug ist im Großlager unersetzlich, steigert aber auch die Unfallquote. Abstürzende Ladungen, versehentliches Anfahren von Menschen, umstürzende Fahrzeuge und generelles Fehlverhalten sind die wichtigsten Gefahrenquellen. Durch die Installation von Anfahr- und Rammschutz und die Bereithaltung ausreichend breiter Fahrtwege lassen sich die Gefahren minimieren. Wichtig ist außerdem, dass Flurförderfahrzeuge ausschließlich von Personen mit gültigem Führerschein (z.B. Staplerschein) betrieben werden. Für nicht führerscheinpflichtige Fahrzeuge ist eine sorgfältige Weisung in die Handhabung Pflicht.
Wichtig: Regelmäßige Wartungen sind Pflicht. Einmal täglich sollten alle eingesetzten Fahrzeuge (auch der Handhubwagen) einer Sichtkontrolle unterzogen werden. Defekte sind umgehend zu beheben, um die Sicherheit aufrechtzuerhalten.
Zeitmanagement gegen Hektik und Unfallgefahren
Zeitdruck ist eine bekannte Unfallquelle, da die Fehlerquote in hektischen Situationen ansteigt. In Lagern herrscht oft ein zu knappes Zeitfenster, um alle anfallenden Arbeiten zu erledigen. Infolgedessen geraten Mitarbeiter unter Druck und versuchen, all ihre Aufgaben in der vorgegebenen Zeit zu erledigen.
Darunter leidet nicht nur die Qualität (minderwertig verpackt, vergessenes Packmaterial etc.), sondern auch das Sicherheitsbewusstsein. Wird zugunsten der Uhr auf das Tragen von Schutzkleidung, die Einhaltung von Sicherheitsvorkehrungen und die Ergonomie verzichtet, hat das negative Einflüsse auf das Gefährdungspotenzial.
Unterweisungen und Schulungen für Mitarbeiter
Die Fehlerquelle Mensch ist noch heute eine der größten Herausforderungen in der Logistik. Durch zunehmend digitale und automatisierte Prozesse reduziert sich die Zahl zwar, nach wie vor ist Unachtsamkeit aber ein Risikofaktor. Umgehen lässt er sich durch Awareness für drohende Gefahren. Eine einmalige Unterweisung reicht nicht aus, um das Bewusstsein für den sorgfältigen Umgang mit Arbeitsmaterialien zu schärfen. Insbesondere im Handling von bestimmten Werkzeugen, bei der Nutzung von Maschinen oder Flurförderfahrzeugen sind regelmäßige Schulungen von Bedeutung.
Ausstattung der Arbeitsplätze für Lagerarbeiter
Lagerarbeit ist körperlich anstrengend und belastend. Optimale Arbeitsbedingungen reduzieren die Ablenkungsquote und die Gefahren für die eigene Gesundheit. Regelmäßige Erholungszeiten sind Pflicht, auch die Nutzung von Automatisierungsmöglichkeiten zeigt sich als sehr sinnvoll. Verpflichtend ist zudem die Anpassung der Schutzausrüstung auf Basis der Gefährdungsbeurteilung. Um Schäden im Bewegungsapparat zu minimieren, ist auch bei Lagerarbeitsplätzen auf Ergonomie zu achten.
Effiziente Nutzung von Regalsystemen für die Sicherheit
Regale im Großlager müssen gesetzliche Vorschriften einhalten. Ein Hauptaugenmerk liegt auf der maximalen Feld- und Fachlast, die nicht überschritten werden darf. Sobald ein Regal gewerblich genutzt wird, unterliegt es der Prüfungspflicht. Arbeitgeber sind dazu verpflichtet, Sichtkontrollen in engen Abständen vorzunehmen.
Ist die Unversehrtheit eines Regals nicht mehr gewährleistet, ist ein sofortiger Austausch zum Schutz der Mitarbeiter erforderlich. DIN EN 15635 regelt die gesetzlichen Vorschriften für Wartung und Anwendung von Stahlregalsystemen und anderen Lagereinrichtungen.
Fazit: Gefahrenvermeidung im Großlager als Herausforderung
Lagerhallen sind eine Gefahrenquelle für Mitarbeiter und Besucher. Wie hoch die Wahrscheinlichkeit von Unfällen ist, hängt stark von den Sicherheitsvorkehrungen ab. Arbeitgeber sind verpflichtet, Betriebssicherheitsverordnung, Arbeitsschutzgesetz und Arbeitsstättenverordnung einzuhalten.
In der Lagerhaltung gibt es spezielle DIN-Normen, die klare Regeln für die Nutzung von Regalsystemen, Bediengeräten und Flurförderzeugen beinhalten. Ein klar strukturiertes Lager mit Gefahrensymbolen und Schutzeinrichtungen ist als sicherer Arbeitsort für Logistiker unverzichtbar.