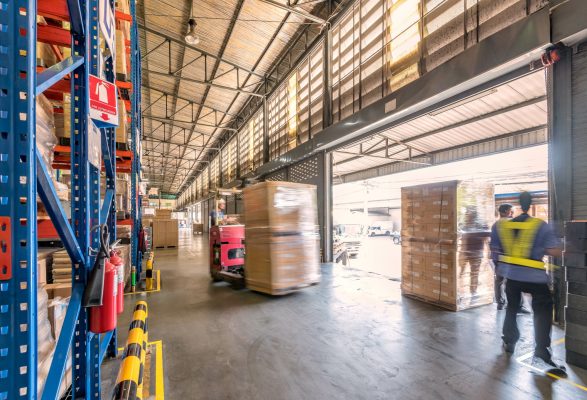
Lagerhaltung: Aufgaben, Ziele, Lagerarten und -Strategien
- Was versteht man unter Lagerhaltung?
- Was sind die Ziele der Lagerhaltung?
- Was sind die Aufgaben der Lagerhaltung im Unternehmen?
- Welche Funktionen hat die Lagerhaltung?
- Welche Strategien werden in der Lagerhaltung eingesetzt?
- Welche Lagerarten gibt es?
- Warum ist die Lagerhaltung wichtig?
- Welche Kosten entstehen bei der Lagerhaltung?
Was versteht man unter Lagerhaltung?
Der Begriff Lagerhaltung kann als die Verwaltung und Aufbewahrung von Gütern aller Art definiert werden. Die Lagerhaltung von Produkten und Waren kann an einem separaten Lagerplatz, bei einem externen Logistikunternehmen oder direkt in der Fertigung erfolgen. Wesentliche Aspekte der Lagerhaltung betreffen die Pflege der gelagerten Artikel und die Planung und Verwaltung der Bestände. Lagerhaltung kann sowohl für kurze Zeiträume (z. B. bei saisonalen Produkten) und ebenso für längere Abschnitte (z. B. bei Rohstoffen) erforderlich sein.
Was sind die Ziele der Lagerhaltung?
Unternehmen, die ein Lager unterhalten und Waren verwalten, verbinden mit der Lagerhaltung verschiedene Ziele:
Ziele der Lagerhaltung | Ausprägung |
Hohe Lieferzuverlässigkeit | Durch eine vorausschauende Lagerhaltung ist sichergestellt, dass die produzierten Produkte des Unternehmens zu jeder Zeit zur Verfügung stehen. Liefertreue ist einer der wesentlichen Parameter für Großhandelspartner oder Endkunden. |
Geringe Lieferzeiten | Mit professionellen Lagerstrategien kann „just-in-time“ produziert werden, ohne einen großen Lagerbestand vorzuhalten. Dieser Wettbewerbsvorteil ist in globalisierten Märkten essenziell. |
Optimiertes Kosten-Nutzen-Verhältnis | Eine wesentliche Lagerstrategie fokussiert sich darauf, die für die Produktion wesentlichen Teile einzulagern. Besteht ein Lagerbestand bei selten benötigten Waren, steigen die Lagerhaltungskosten. |
Moderne Kommunikations- und Informations-Vernetzung | Alle an der Supply Chain beteiligten Firmen sollten vernetzt agieren. Moderne Software-Applikationen und Lagerverwaltungssysteme informieren Lieferanten in Echtzeit über Lagerbestände, sodass bei einer Unterdeckung von Produkten automatisiert nachgeliefert werden kann. |
Lieferqualität | Die Produktion qualitativ hochwertiger Produkte ist die Grundlage für langfristigen Erfolg. Die Lieferqualität sollte sich aus diesem Grund an den Qualitätsnormen der ISO 9000 ff orientieren, die sich auf Qualitätsmanagement-Systeme und Prozessmodelle beziehen. Professionelle Lagerhaltung hat einen entscheidenden Einfluss auf die Lieferqualität. |
Lieferflexibilität | Flexible Unternehmen reagieren umgehend auf die Anforderungen ihrer Kunden. Ist die Lagerhaltung zukunftsorientiert und vernetzt aufgebaut, sind veränderte Auftragsmengen, verkürzte Lieferzeiten oder strengere Qualitätsvorschriften in kurzer Zeit realisierbar. |
Was sind die Aufgaben der Lagerhaltung im Unternehmen?
Ein Lager hat die übergeordnete Aufgabe, die Bereitstellung und Versorgung der Fertigung mit Waren und Produkten in der geforderten Quantität, Qualität und im definierten Zeitrahmen sicherzustellen. Weitere wichtige Aufgaben in einem Lager beziehen sich zum Beispiel auf:
- Die Lagerung am korrekten oder vorab definierten Lagerplatz,
- die Beachtung der gesetzlichen Bestimmungen bei der Lagerung von Gefahrenstoffen,
- das Einlagern von Waren nach Parametern wie Verfallsdatum, Temperatur oder Luftfeuchtigkeit,
- die intensive Prüfung der Waren vor der Lagerung,
- regelmäßige Inventuren, um den Lagerbestand jederzeit zu kennen,
- das Auslösen von Bestellungen,
- das Finden und Kommissionieren der Waren im Lager,
- administrative Vorgänge wie Drucken von Versandetiketten, Rechnung und Lieferscheinen sowie
- die Lagerbuchführung (in der Regel ausgeführt durch die Lagerverwaltung),
- die Bereitstellung der Waren zur Abholung (Warenausgang).
Welche Funktionen hat die Lagerhaltung?
Die Funktionen der Lagerhaltung sind vielfältig und unternehmensspezifisch. In der Lagerlogistik unterscheidet man grundsätzlich die folgenden Funktionen:
- Sicherungs- oder Versorgungsfunktion: Durch eine zielorientierte und vorausschauende Lagerung kann die Produktion von Waren im Unternehmen sichergestellt werden. Ebenfalls essenziell ist, dass die hergestellten Produkte über den Warenausgang des Lagers an die Kunden ausgeliefert werden.
- Ausgleichs- und Pufferfunktion (Überbrückungsfunktion): Die Lagerlogistik hat die Funktion, bei Abweichungen zwischen der Bestands- und Absatzmenge oder bei einer Diskrepanz zwischen der Beschaffungs- und Produktionsmenge einzuspringen und der Produktion benötigte Roh- oder Hilfsstoffe zuzuführen. Die Überbrückungsfunktion in der Lagerlogistik sichert die Produktion auch in Zeiten, in denen bestimmte Waren auf regionalen Märkten oder dem Weltmarkt schwer zu beschaffen sind. Als Beispiel kann die Corona-Pandemie angeführt werden, in der Lieferketten unterbrochen wurden und eine Ausgleichs- und Pufferfunktion in der Lagerverwaltung essenziell war.
- Sortierfunktion: Alle Waren, Artikel und Güter, die im Lager deponiert werden, müssen nach internen Vorgaben in spezielle Regale sortiert und klassifiziert und in den Lagerbestand überführt werden.
- Veredelungsfunktion: Direkt nach der Herstellung können Artikel und Waren durch eine zeitlich gestreckte Lagerung veredelt werden. In der Nahrungsmittelproduktion werden beispielsweise Käse, Wurstwaren oder Wein über Monate oder Jahre fachgerecht gelagert und vor dem Verkauf veredelt.
- Umformungsfunktion: Diese produktionswirtschaftliche Lageraufgabe hat das Ziel, Waren, die im nicht bearbeitungsfähigen Zustand angeliefert wurden, so zu präparieren, dass sie in der Produktion verwendet werden können. Dies geschieht durch Re-Konfektionierung, Sortierung oder das Mischen verschiedener Güter und Waren.
- Spekulationsfunktion: Logistiker und Lagerverantwortliche beobachten die Märkte und sind mit Lieferanten vernetzt. Steigen zum Beispiel Preise für Rohwaren oder Güter auf Märkten, schließen sie langfristige Verträge zu den bestmöglichen Konditionen ab oder kaufen Waren oder Materialien vorausschauend ein, bei denen auf lange Sicht mit steigenden Preisen zu rechnen ist. Diese Art der vorausschauenden Planung wird fachlich als Spekulationsfunktion bezeichnet.
- Darbietungsfunktion: Die Darbietungsfunktion stellt den Übergang von der Lagerhaltung in den Verkaufsvorgang dar. Vor allem im Einzelhandel wird die Darbietungsfunktion regelmäßig genutzt, um Kunden die Waren direkt im Verkaufslager zu präsentieren. Im Großhandel ist die Darbietungsfunktion ebenfalls bekannt. Ein prominentes Beispiel sind regionale Großmärkte wie Blumen oder Obst und Gemüse, in denen Einzelhändler die Ware direkt vom Großhändler erwerben und begutachten können.
Welche Strategien werden in der Lagerhaltung eingesetzt?
Eine professionelle Lagerhaltung muss strategisch aufgebaut sein. Erst dann entfalten sich die spezifischen Vorteile einer durchdachten Lagerhaltung. Vor allem in großen Lagern, in denen täglich ein umfangreicher Materialfluss feststellbar ist, haben Kommissionierer und die Lagerverwaltung die Aufgabe, Strukturen und Strategien zu implementieren, die das Lagervolumen effektiv nutzen und Schnelligkeit und Kosteneffizienz garantieren. Man unterscheidet folgende strategische Obergruppen:
- Bewegungsstrategie.
- Belegungsstrategie.
- ABC-Lagerstrategie.
Die Bewegungsstrategie
Der Begriff Bewegungsstrategie bezieht sich auf die Organisation der Bewegung von Gütern und Waren in einem Lager. Die Bewegungsstrategie in der Lagerhaltung sollte in einer Weise aufgebaut werden, dass Waren und Artikel so effizient wie möglich bewegt werden, um Zeit und Kosten zu sparen. Oberstes Ziel bei der Bewegungsstrategie ist ein maximaler Warendurchsatz im Lager. Eine zielführende Bewegungsstrategie ist wichtig, um ein Lager effektiv zu verwalten. Zu den Unterkategorien der Bewegungsstrategie gehören:
Zuförderstrategie | Ein Förderband transportiert Waren in Zyklen oder individuell und schubweise in die verschiedenen Gänge des Lagers und an die Lagerplätze, wo diese Waren anschließend in die Regale eingeordnet werden. |
Abförderstrategie | Einsatz einer sogenannten Auslagerstichbahn. Waren, die dringend benötigt werden, erhalten Vorrang. |
Einzelspielstrategie | Fokus auf Einlagerung oder Auslagerung der Waren. Das Ein- und Auslagern wird nicht gleichzeitig, sondern nacheinander durchgeführt. |
Doppelspielstrategie | Kombination der Vorgänge Einlagern und Auslagern von Waren. Vorteil dieser Strategie ist das Minimieren von Leerfahren im Lager. |
Umlagerstrategie | Wird ein Lagerplatz für einen bestimmten Artikel benötigt, müssen vorhandene Waren auf diesem Lagerplatz umgelagert werden. |
Gangwechselstrategie | Die Gangwechselstrategie ist eine Bewegungsstrategie, bei der die Artikel so bewegt werden, dass sie immer auf derselben Seite des Lagers bleiben. Diese Strategie wird verwendet, um die Bewegung der Waren zu vereinfachen und Zeit und Kosten zu sparen. |
Fahrwegstrategie | Die Fahrwegstrategie verfolgt das Ziel, die Waren so zu bewegen, dass Waren auf dem kürzesten Weg zum Zielort bewegt werden. |
Die Belegungsstrategie
Als Belegungsstrategie werden Verfahren in der Lagerhaltung bezeichnet, bei denen Zeit und Kosten durch optimales Ausnutzen der Lagerplätze und kurze Wege eingespart werden. Zu den wichtigsten Belegungsstrategien im Lagerumfeld gehören:
FEFO – First Expired – First Out | FEFO ist eine Belegungsstrategie, bei der die Güter nach Produktions- oder Ablaufdatum gelagert werden. Diese Strategie wird vor allem in der Lebensmittelindustrie verwendet, um sicherzustellen, dass Waren nicht verderben, bevor sie an den Kunden ausgeliefert werden. |
FIFO – First In – First Out | FIFO bezeichnet die am häufigsten verwendet Lagerstrategie, bei der Lagerartikel, die als erstes eingelagert wurden, ebenfalls als erstes ausgelagert werden. |
LIFO – Last In – First Out | Bei der LIFO-Lagerstrategie werden die zuletzt eingelagerten Waren zuerst ausgelagert. LIFO kann zum Beispiel in kleinen Lägern oder für Produkte genutzt werden, die sich nicht verändern, beispielsweise Waren wie Möbel, Baumaterialien oder Plastikartikel. |
HIFO – Highest In – First Out | Waren mit dem höchsten Wert oder Verkaufspreis werden bei der HIFO-Lagerstrategie zuerst ausgelagert. |
LOFO – Lowest In – First Out | Im Gegensatz zur HIFO-Lagerstrategie werden bei LOFO die Waren zuerst ausgelagert, die den geringsten Wert haben. |
Chaotische Lagerhaltung | Die sogenannte chaotische Lagerhaltung bezieht sich auf eine Belegungsstrategie, bei der die Artikel in zufälliger Reihenfolge gelagert und bewegt werden. Diese chaotische Strategie wird verwendet, um die Kapazitäten des Lagers optimal auszunutzen. |
Schnellläuferkonzentration | Schnellläuferkonzentration bedeutet, sich in der Logistik auf Waren und Artikel zu konzentrieren die am häufigsten verkauft werden. Diese Waren müssen schnell ein- und ausgelagert werden können. |
Zusätzlich können im Bereich der Belegungsstrategie freie oder feste Lagerplätze, eine zonenweise feste Lagerordnung oder eine artikelreine Platzbelegung zur Anwendung kommen. Welche Lagerstrategien gewählt werden, hängt von der Ware, der Lagergröße, der Lagerzeit der Produkte und weiteren betriebsspezifischen Parametern ab.
ABC-Lagerstrategie
Bei der ABC-Lagerstrategie werden alle Waren und Produkte aufgrund ihrer Umschlaghäufigkeit in die Kategorien A, B und C eingeteilt. Die klassifizierten Produkte erhalten im Lager einen eigenen Lagerbereich und werden so positioniert, dass ein schnelles und kosteneffizientes Kommissionieren gewährleistet ist.
Welche Lagerarten gibt es?
Es gibt unterschiedliche Lagerarten in Unternehmen. Man unterscheidet vor allem zwischen folgenden Lagerarten:
- Distributionslagern, die in räumlicher Nähe zu potenziellen Kunden liegen,
- Zwischen- und Pufferlagern, in denen halbfertige Erzeugnisse gelagert werden,
- Umschlags- oder Transitlager, das der Zwischenlagerung dient,
- Beschaffungs- oder Produktionslager, in dem die für die Produktion notwendigen Waren gelagert werden,
- Vorratslager, in dem Waren als Puffer gelagert werden sowie
- Kommissionierlager, in dem Waren für die Auftragskommissionierung untergebracht sind.
Warum ist die Lagerhaltung wichtig?
Die Lagerhaltung ist für Unternehmen wichtig, weil sie die Lieferkette und Materialfluss aufrechterhält und den Produktionszyklus sicherstellt. Ebenfalls ist die Lagerverwaltung essenziell, um die Qualität der Produkte sicherzustellen und Kosten zu sparen. Eine vorausschauende Lagerhaltung ermöglicht es Unternehmen, neue Märkte zu erschließen und die Nachfrage nach ihren Produkten zu steigern. Lagerhaltung ist aus diesem Grund ein wesentlicher Bestandteil des unternehmerischen Erfolgs.
Welche Kosten entstehen bei der Lagerhaltung?
Die Kosten für die Lagerhaltung von Gütern können sich aus verschiedenen Komponenten zusammensetzen. Zu den wichtigsten Kostenkomponenten gehören:
- Kosten für das Lagerhaus oder die Lagerfläche: Die Kosten für die Lagerfläche beziehungsweise das Lagerhaus hängen in erster Linie vom Flächenbedarf ab und steigen mit der Größe des Lagers proportional an.
- Kosten für die Lagerausrüstung und Lagerverwaltung: Zur Lagerausrüstung gehören unter anderem Regale, Kisten Paletten und Flurförderfahrzeuge, Transportbänder sowie technisches Equipment.
- Lohnkosten für die Angestellten im Lager: Die Kosten für die Lagerarbeiter setzen sich in der Regel aus den Gehältern und den Sozialabgaben sowie aus Schulungs- und Ausstattungskosten zusammen.
Die Kontrolle und stetige Optimierung der Kosten im Lager erfolgt durch die Lagerverwaltung.