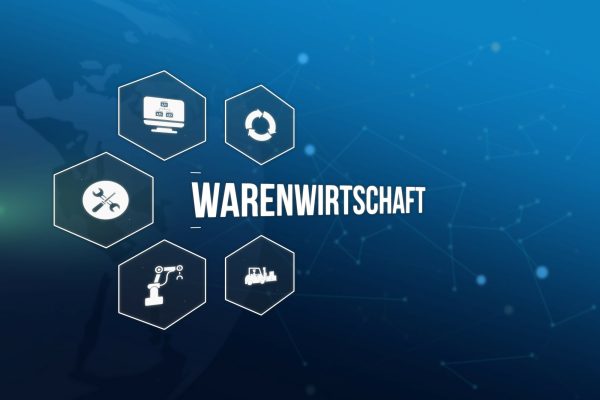
Warenwirtschaft: Definition, Aufgaben & Vorteile von Warenwirtschaftssystemen
- Was ist Warenwirtschaft?
- Welche Ziele verfolgt die Warenwirtschaft?
- Was sind die Aufgaben der Warenwirtschaft?
- Was umfassen die Bereiche der Warenwirtschaft?
- Überschneidungen der Warenwirtschaft und Logistik
- Was ist ein Warenwirtschaftssystem?
- Welche Funktionen bieten Warenwirtschaftssysteme?
- Welche Arten von Warenwirtschaftssystemen gibt es?
- Was sind die Vorteile eines Warenwirtschaftssystems?
- Was ist der Unterschied zwischen einem Warenwirtschaftssystem und einem ERP-System?
- Welchen Unterschied gibt es zwischen Warenwirtschaft und Materialwirtschaft?
Was ist Warenwirtschaft?
Die Warenwirtschaft beschäftigt sich als Teil der Betriebswirtschaft mit der Verwaltung und Verteilung von Waren, insbesondere im Hinblick auf die Produktion, Lagerhaltung und den Vertrieb. Die Warenwirtschaft ist eine der Kernaufgaben in jedem Unternehmen und umfasst die Planung, Steuerung und Kontrolle aller Aktivitäten, die mit dem Umgang von Waren zusammenhängen. Die Warenwirtschaft hat zum Ziel, die Ressourcen im Betrieb so effizient wie möglich zu nutzen und durch Prozessoptimierung Kosten zu sparen.
Welche Ziele verfolgt die Warenwirtschaft?
Die Ziele der Warenwirtschaft sind eng mit den Unternehmenszielen verknüpft. Zum einen fokussiert sich die Warenwirtschaft darauf, die materielle Liquidität des Unternehmens zu erhalten. Das bedeutet, dass grundsätzlich genügend Waren und Produkte für die Produktion zur Verfügung stehen, die qualitativ hochwertig und preislich attraktiv sind.
Da Rohmaterialien und andere Güter das Kapital des Unternehmens binden, verfolgt die Warenwirtschaft ebenfalls das Ziel, die Prozesse im Wareneingang zu optimieren und die Lagerhaltung auf das notwendige Minimum zu reduzieren.
Was umfassen die Bereiche der Warenwirtschaft?
Jeder Bereich nimmt eine andere wichtige Funktion im Rahmen der Warenwirtschaft ein und ist für unterschiedliche Aufgaben zuständig.
Was beinhaltet der Wareneinkauf?
Der Einkauf gehört zu den zentralen Fachabteilungen im Unternehmen. Neben dem kurzfristigen, operativen Einkauf von Waren und Dienstleistungen übernimmt der strategische Einkauf folgende Aufgaben:
- Aufbau langfristiger Partnerschaften mit Lieferanten,
- Integration von Einkaufsprozessen in den Betrieb, die die Bedarfsermittlung und das Bestellwesen automatisieren,
- das Einholen von Angeboten verschiedener Lieferanten und der Angebotsvergleich,
- Vergleich der Preise, der Qualität und der Lieferfristen,
- Aushandlung der besten Konditionen mit Lieferanten.
Welche Funktion hat der Wareneingang?
Die Aufgaben der Wareneingangsabteilung bestehen darin,
- die eingehenden Waren zu entladen, zu kontrollieren und zu registrieren sowie
- die Lagerung und Verteilung der Waren zu organisieren.
Bei Problemen mit der Qualität oder Güte der Waren liegt es in der Verantwortung der Warenannahmeabteilung, diese zu beheben, indem Reparaturen und Ersatzlieferungen veranlasst werden.
Welche Aufgaben übernimmt die Lagerhaltung?
Der Lagerhaltung kommt eine entscheidende Rolle in der Warenwirtschaft zu. Unter anderem werden im Lager des Betriebs die Lagerbestände verwaltet und die im Produktionsprozess gefertigten Produkte an die Kunden ausgeliefert. Darüber hinaus spielt das Lager eine wichtige Rolle bei der Qualitätskontrolle der Produkte und bei der Auftragsabwicklung. Sie dient dazu, dem Unternehmen einen reibungslosen Ablauf der Warensicherung zu ermöglichen.
Was sind die Aufgaben des Vertriebs?
Das Ziel des Vertriebs besteht darin, Produkte zu verkaufen und Einnahmen zu generieren. Um dies zu erreichen, müssen die Verkaufsteams verschiedene Aufgaben übernehmen:
- die Ermittlung der Kundenbedürfnisse,
- die Entwicklung von Marketingstrategien,
- Preisverhandlungen und Geschäftsabschlüsse.
Zudem geben die Verkaufsteams den Warenmanagern Feedback zu Kundentrends und -präferenzen, um künftige Produktangebote noch bedürfnisgerechter zu konzipieren. Durch die enge Zusammenarbeit von Vertrieb und Warenwirtschaft kann sichergestellt werden, dass die Produkte den Kundenwünschen entsprechen und einen maximalen Umsatz erzielen.
Was sind die Funktionen des Warenausgangs?
Der Warenausgang kümmert sich um die Versorgung des Kunden oder Partners mit den bestellten Waren und Gütern aus dem Lager. Folgende Funktionen übernimmt der Warenausgang:
- die Bereitstellung und Verpackung der Güter,
- die Kontrolle der ausgehenden Waren,
- die Verladung beziehungsweise der Versand der Güter.
Überschneidungen der Warenwirtschaft und Logistik
Mehrere Bereiche der Warenwirtschaft weisen Überschneidungen zur Logistik auf und können nicht immer klar voneinander getrennt werden. Der Bereich der Logistik übernimmt die Organisation der Bewegung von Waren – sowohl bei der Beschaffung, Lagerung und dem Versand zu dem Kunden – und spielt demnach eine wichtige Rolle bei der Material- und Warenwirtschaft.
Was ist ein Warenwirtschaftssystem?
Ein Warenwirtschaftssystem, das häufig mit den Abkürzungen WaWi oder WWS abgekürzt wird, versteht man eine Sammlung von spezifischer Software, die Unternehmen darin unterstützen, den Warenfluss im Betrieb professionell zu steuern. Das Ziel einer Warenwirtschaftssoftware ist es, sicherzustellen, dass ein Unternehmen seine Lagerbestände effizient verwalten kann und die richtigen Produkte zur richtigen Zeit verfügbar sind. Ein WWS deckt in den meisten Fällen die Unternehmensbereiche Verkauf, Einkauf, Wareneingang, Warenausgang und Lagerverwaltung, aber auch die Inventur ab.
Welche Funktionen bieten Warenwirtschaftssysteme?
Ein Warenwirtschaftssystem ermöglicht es:
- Bestellungen aufzugeben,
- Lieferanten zu managen und
- das Inventur zu überwachen.
Moderne Software für die Warenwirtschaft bieten ihren Anwendern darüber hinaus weitere integrierte Lösungen an, beispielsweise Analysetools, um spezifische Daten zum Lagerbestand sowie die Bestellhistorie zu überwachen. Derartige Analysen von Daten können Unternehmen dabei helfen, die Effizienz ihrer Lagerbestände zu verbessern und potenzielle Probleme mit Lieferanten oder Bestellungen zu identifizieren.
Einige Warenwirtschaftssysteme bieten optional die Möglichkeit, Online-Bestellungen zu erstellen und dessen Daten zu verwalten. Andere WWS können mit einem integrierten CRM-System, einem Kassensystem oder Lösungen zur Produktionsplanung erweitert werden.
Welche Arten von Warenwirtschaftssystemen gibt es?
Grundsätzlich unterscheidet man zwischen drei Arten von Warenwirtschaftssystemen (WaWi):
- Geschlossenes WWS: Alle betriebswirtschaftlichen Aufgaben werden von einem System übernommen.
- Offenes WWS: Einzelne Funktionen werden durch andere Softwareapplikationen abgedeckt und über Schnittstellen an das WaWi-System angebunden.
- Integriertes WWS: Dieses System nthält zusätzlich externe Schnittstellen zu Lieferanten, Banken oder zum Webshop.
Was sind die Vorteile eines Warenwirtschaftssystems?
WaWi haben je nach Lösung verschiedene Vorteile. Bedeutend sind unter anderem folgende Vorteile:
- Zeitersparnis bei der Konzeption von Angeboten, Aufträgen, Rechnungen, Lieferscheinen und Mahnungen,
- optimierte digitale Lagerverwaltung,
- systematische Pflege der Daten in einem Grundsystem,
- Transparenz durch Echtzeitauswertungen,
- integriertes Kundenbeziehungsmanagement (CRM),
- Abrufen tagesaktueller Statistiken und Daten zur Sortimentsoptimierung,
- Möglichkeit, die Produktionsplanung in das WaWi zu integrieren.
Was ist der Unterschied zwischen einem Warenwirtschaftssystem und einem ERP-System?
Die Unterschiede zwischen einem Warenwirtschaftssystem und einem ERP-System [Enterprise Resource Planning] sind vielfältig. Warenwirtschaftssoftware dient der Unterstützung beim Verkauf von Produkten, da es die Warenbewegungen organisiert. ERP-Systeme werden im Gegensatz eingesetzt, um die Gesamtressourcenplanung abzubilden.
ERP-Systeme bieten aus diesem Grund mehr Funktionen und Lösungen als Warenwirtschaftssysteme und sind komplexer aufgebaut. ERP-Systeme automatisieren und verwalten Prozesse in allen relevanten Unternehmensbereichen. Eines der bekanntesten ERP-Software-Systeme ist SAP S/4HANA. Dieses ERP-System analysiert und optimiert zukunftsorientiert und unter Einsatz von KI und maschinellem Lernen Geschäftsprozesse.
Welchen Unterschied gibt es zwischen Warenwirtschaft und Materialwirtschaft?
Die Begriffe Warenwirtschaft und Materialwirtschaft haben auf den ersten Blick manche Schnittstellen. Gleichzeitig findet man viele Unterschiede zwischen der Warenwirtschaft und der Materialwirtschaft.
Zunächst einmal ist die Warenwirtschaft ein Teil der strategischen Unternehmensplanung in Handelsunternehmen und steuert den Warendurchfluss, während die Materialwirtschaft operativ die Versorgung der Produktion übernimmt. Während der Fokus der Warenwirtschaft auf dem Management von Gütern und Rohwaren liegt, konzentriert sich Materialwirtschaft auf den Einkauf und die Lagerhaltung von Materialien.